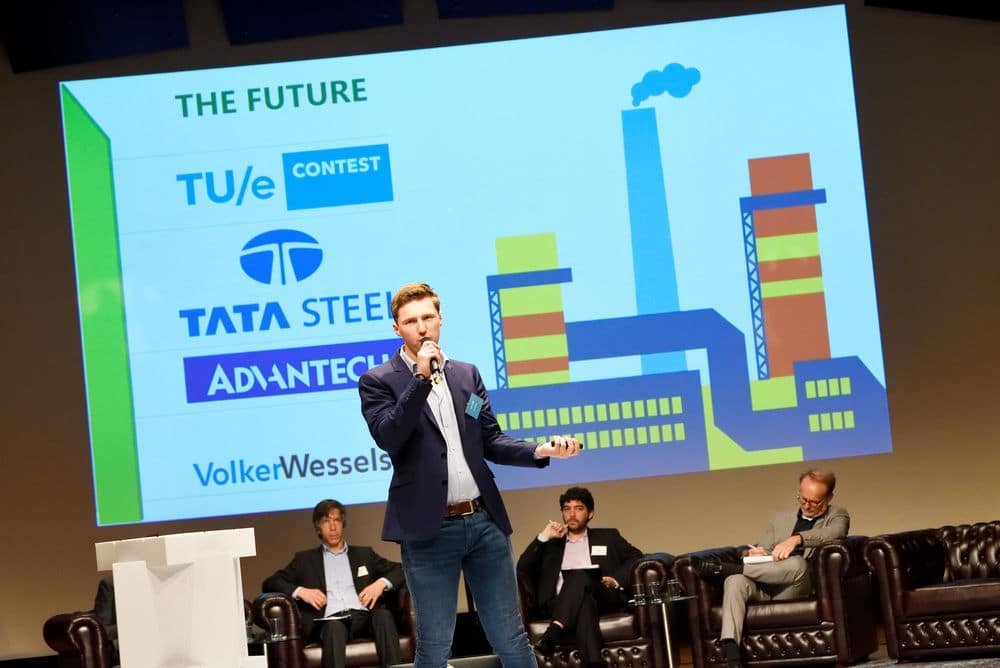
The manufacture of batteries, telephones, laptops and other electronics is continually on the rise. The mountain of electronic waste is also expanding. Thousands of kilos of recyclable metals are currently being dumped in landfills. The CORE student team at the Technical University of Eindhoven (TU/e) has developed a relatively simple process aimed at bringing these metals back to their purest state. They can be recycled this way and the supply of metal will become unlimited.
The earth has its own process for recycling waste. For example, waste ends up in rivers via contaminated air and eroded rocks. These rivers bring it out to the ocean where it slowly sinks down to the bottom of the sea. There it gradually disappears between the cracks in the tectonic plates under the seabed into the earth’s core. There it is so hot that the materials disintegrate back into pure elements. The core pushes those elements, such as metals, back to the earth’s crust where people are able to mine these. This process takes 35 million years. And that is far too lengthy a process for meeting the current demands of industry. In 35 years’ time, for instance, lithium and cobalt will be depleted. “That’s why we’ve developed an incinerator where this process can be carried out in about one week,” says Dirk van Meer, captain of Team CORE.
Children with lead poisoning
Recycling metals in this way is not restricted to the production of electronics. It also solves a social problem. “Old phones and computers are currently mainly being sent to Africa and China. There, small children are forced to take out any useful parts in order to be able to sell them,” says Van Meer. “The combustion process which is used to destroy the electronics causes the rivers to become acidic. The children often suffer from lethal levels of lead poisoning.”
These scenes are a thing of the past thanks to the recycling factories set up by the Eindhoven student team. They want to set each province up with its own factory equipped with this kind of recycling incinerator. “Then the waste won’t have to be transported very far. That makes a big difference in terms of environmental pollution and costs.” Construction work on the first factory will start at the end of 2020 in Duiven. This site will mainly process waste generated by the recycling of automobiles. At the moment, the team is actively involved in preparation, e.g. with arranging environmental permits. “We always provide multidisciplinary teams wherein enthusiastic students as well as experienced professionals from the industry get to work together.”
Following the factory in Duiven, the student team aim to build a factory on the Metalot site in Budel, also in the Netherlands. “We are planning to process tougher waste streams there, such as batteries,” he says.
From waste to pure elements
Energy-rich waste, such as sludge, and low-energy waste, such as metal, are mixed together in the electric incinerators. ” This means that we only have to switch on the incinerator once and then it will remain warm because of the energy from the waste,” explains the chemical technology student. “In addition, it allows us to process a variety of waste materials that are normally useless to industry.” Team CORE has a partnership with Auto Recycling Nederland (ARN). ” A fraction of a car remains after recycling. We are able to process this in our machine.” Products such as scrap vehicles, telephones and laptops are first crushed into particles of about one centimeter, then they go into the incinerator.
The incinerator then separates these waste products into pure elements. This creates three layers: metal, sludge and mineral layers. “In principle, it’s all about the metal. New products can be made from these elements.” The team has also sought new applications for the sludge and the mineral layers. “Various residues such as rubber are incorporated into the sludge. This is similar to tar,” says Van Meer. That’s why sludge is frequently used in the construction industry. “The sludge from various metal mills is already being used in construction. There is more than enough demand for us to bring our sludge there too.”
Stones absorb CO2
The mineral layer is mainly made up of obsidian. This is a rock that is formed during a volcanic eruption when lava cools down too quickly. “This substance is capable of absorbing CO2 into its structure. We are therefore able to potentially use it in the top layer of roads. It absorbs part of the CO2 emissions from cars, for example. Moreover, the rock remains 1.5 degrees warmer than present-day asphalt. That will greatly reduce the amount of road salt used during winter.”
Circular economy
Subsequently, this is how the CORE team contributes in various ways to a circular economy. This is also a major dream for team captain van Meer. According to him, a circular production will only be achievable if companies decide to work together. “We want to deal with waste products that other companies don’t do anything with or don’t benefit from. By working together with us, the status of companies that normally do nothing with these waste products will also improve. They will be able to say that they are working in a more sustainable way,” he says. “I don’t see the point of competition in this area. There is still so much to do which nobody else is doing.”
All the factories with the recycling incinerators that the CORE team wants to set up will also be operated by separate companies that are collaborating with one another. For instance, IVER BV will run the factory in the north. “Private investors, such as the Noordelijke Ontwikkelings Maatschappij (NOM, Northern Development Company) and Rabobank will finance the factory over there. Ultimately, a private investor’s company will manage the factory.” A number of students from the student team will get to work in that company. The rest will continue to focus on research. The student team itself is a foundation wherein students will remain involved in the development of the technology.
Challenges for students
Van Meer: ” This is how everyone will be able to further develop their own ambitions and achieve their own goals.” At present, the team is made up of 28 students from a variety of study programs across various academic years. The personal growth of each team member is very important to him. “I want everyone to work on a task that appeals to them. People should enjoy what they do and learn from it at the same time. This is the most important starting point for a student team.” The team is part of TU/e’s innovation Space. A place at the university where students receive supervision during the setting up and running of a student team or a start-up. “There are many experienced people walking around who can support us in all sorts of ways. Aside from that, we also support other teams with the knowledge that we have gained. For instance, when it comes to grant applications.”
There is also room for relaxation alongside the hard work. The chairperson sees his team as a group of friends. ” One minute we’re out grabbing a beer together and then the next, we’re busy solving social problems.”