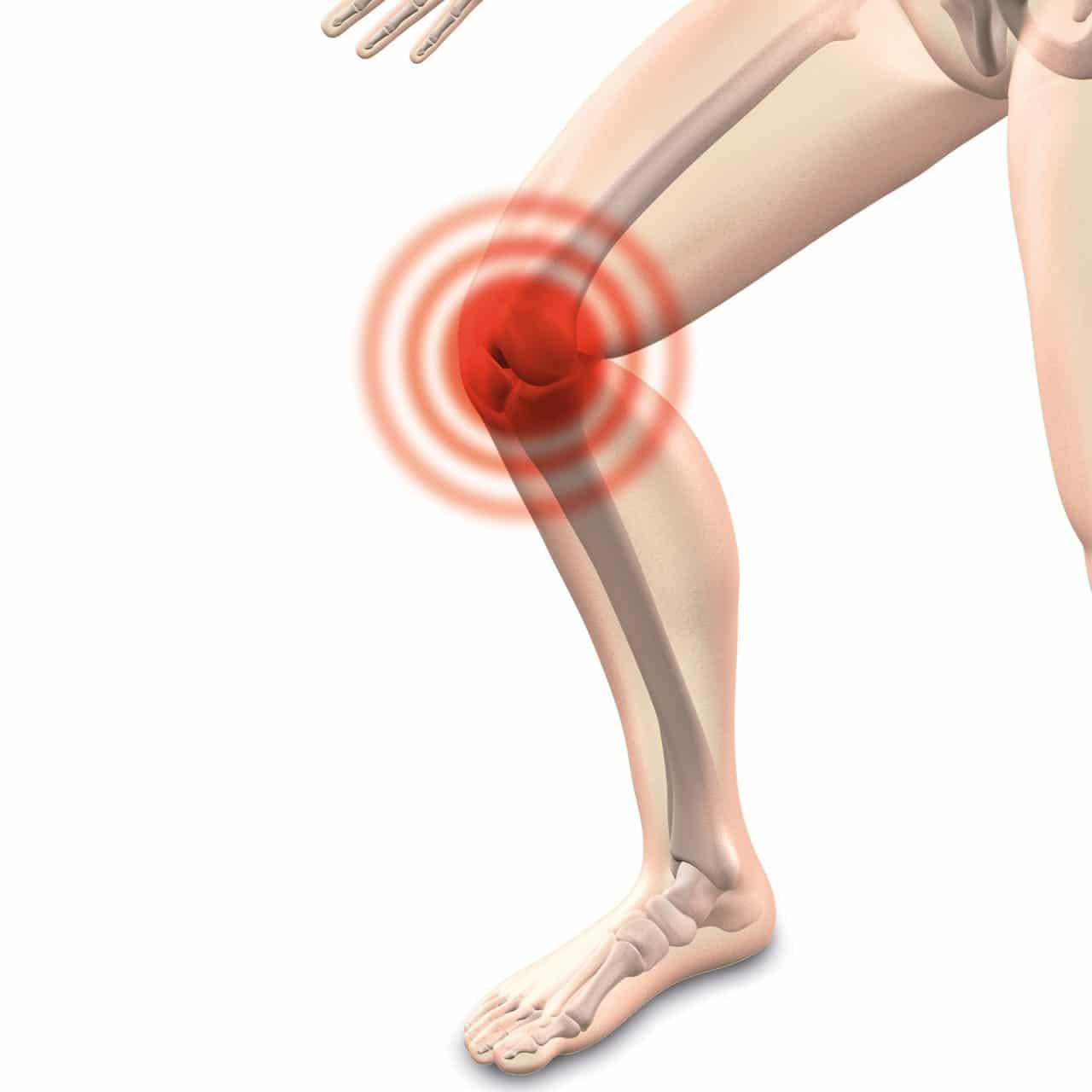
The worst thing a person with osteoarthritis can do to their joints is place too heavy a load on them. Excessive joint load often results in too much strain on the joints and weeks of pain. On the other hand, however, completely relieving those joints is not helpful either. That’s according to sports orthopedist Stefan Sell from the KIT Institute for Sport and Sports Sciences (IfSS) in Karlsruhe, Germany:
“When it comes to the prevention and treatment of osteoarthritis, weight and nutrition are just as important as the right amount of exercise.”
In other words, it’s best if the patient exercises intensively for a certain amount of time every day while at the same time avoiding too much strain. Like taking a brisk walk for several hours.
Training algorithms based on motion data
But how can you accurately assess all of this? Finding the right way to do this isn’t easy. Not too many people are able to interpret their body’s signals correctly without professional support. Perhaps a well-trained athlete might be able to do that.
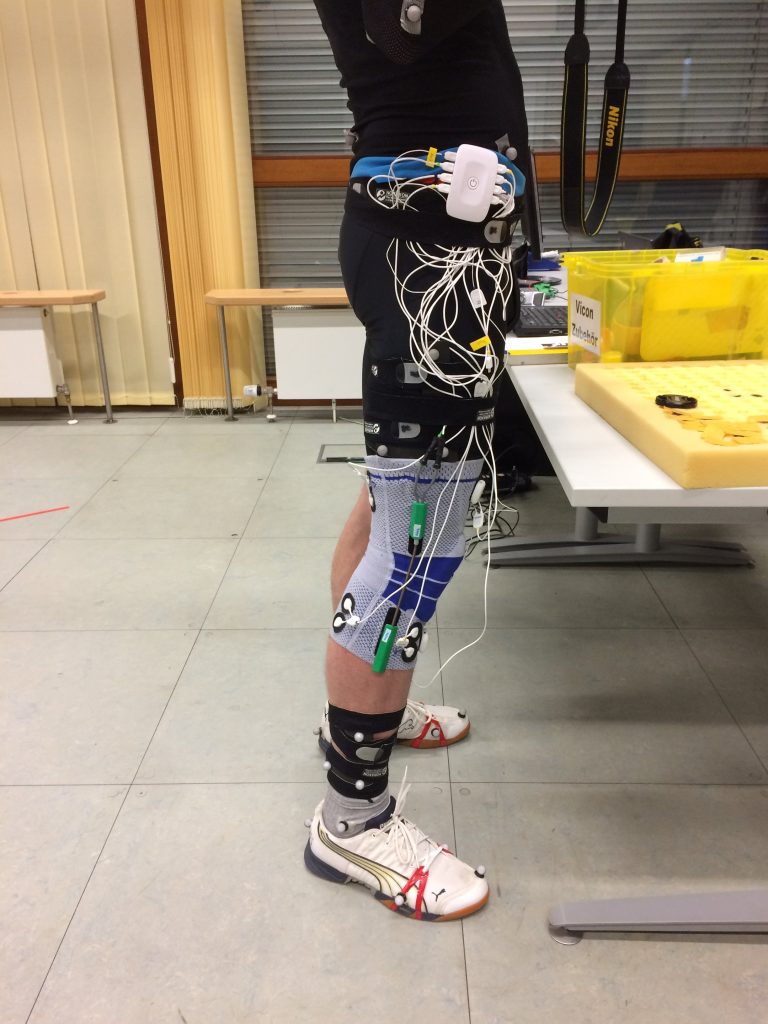
All the more reason for a consortium of sports scientists, doctors, computer scientists and industrial partners to work on a cure for damaged knees. Together they have devised a prototype for a high-tech knee brace. It is equipped with sensors that use self-learning algorithms which are able to measure the load on the knee.
The consortium worked for a total of three years on the intelligent “Anthrokinemat” knee brace. This brace will help osteoarthritis patients in future to properly regulate their day-to-day physical activity. The model is equipped with numerous sensors that collect all relevant data concerning the load on the joint. Even before an osteoarthritis patient exceeds the maximum load level, they will receive alerts on their mobile phone. The aim is to make the patient aware that excessive strain can result in further damage.
Artificial neural networks calculate the joint load level
Professor Thorsten Stein, head of the BioMotion Center, states that the biggest challenge was to find a viable algorithm for quantifying the load on the knee.
“The sensors can only measure motion, not the load itself. However, in the case of osteoarthritis, joints should not be exposed to too much of a load. That’s why we need to be able to assess the forces in the knee as accurately as possible,”, Stein states.
Machine learning algorithms (as in artificial neural networks) are used to solve this problem. This involves training an algorithm with motion data. Over the course of the training process, the algorithm automatically learns to estimate the forces in the knee that are associated with motion.
“Osteoarthritis is a very common disease,” Stefan Sell explains.
According to official statistics, around 35 million people in Germany have radiographic signs of osteoarthritis. About ten million of these people are obviously ill. As joint wear and tear increases with age, one in four German citizens over the age of 50 and about 80% of over-75s will suffer from osteoarthritis. The spine is the most affected area, but osteoarthritis of the knee and hip joints is also widespread.
In certain cases, a physician may be able to provide an OA brace to support the hip, providing relief for osteoarthritis pain. A hip brace is designed to improve mobility and stability, supporting the patient to carry out their daily activities more comfortably. In instances where braces do not provide enough support for hip arthritis, hip replacement surgery may be recommended. According to the Jama Network, ‘the estimated appropriateness rate for a hip replacement was 37.7% in men and 52.7% in women with osteoarthritis.’
Joint project between Unis, BMWi and the company
In the past three years, sports scientists at the Karlsruhe Institute of Technology (KIT) have laid the foundations for the design of the smart brace. They have received funding for their work from the Federal Ministry of Economy and Energy (BMWi). The project partners are the University of Bremen, the manufacturer of amongst other things Bauerfeind orthopedic aids, and the sensor technology company ITP. A prototype is currently under development in another research project.
The Sell and Stein work groups have recently published some of these research results in the Sensors trade journal.