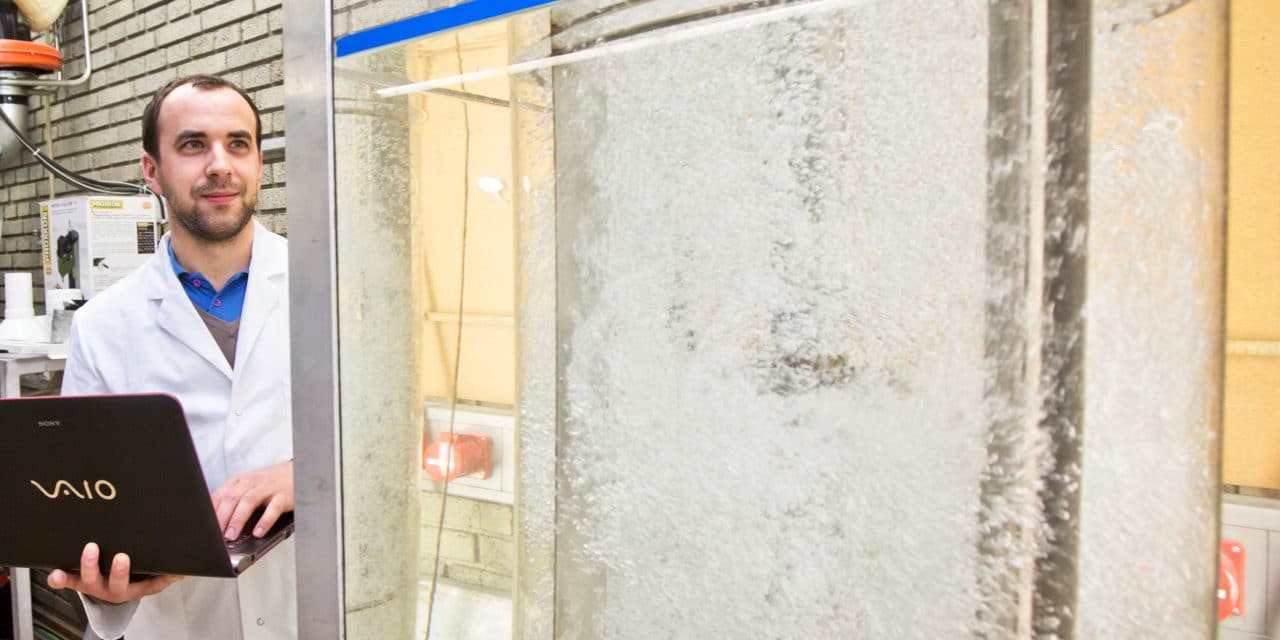
Biopharmaceutical drugs solve previously unsolved problems, but are very complex in their manufacture. A new simulation software will be used to systematize the knowledge process.
Biopharmaceutical drugs lend themselves to treat conditions which cannot be treated with synthetic chemical agents. Examples are multiple sclerosis and anaemia, but also many cancers and rare illnesses. Consequently they are in great demand. According to Graz University of Technology (TU Graz), seven of the ten best-selling drugs are already based on biopharmaceutical active ingredients – in other words, they are genetically engineered.
However, the biopharmaceutical industry still has a major problem when it comes to efficiency. Chemically produced drugs are made up of so-called small molecules and are easily produced in tablet form. Biopharmaceutical preparations are usually comprised of hundreds to thousands of atoms. Their complex manufacturing process is based on microorganisms and is carried out in bioreactors. The knowledge process is limited. Experiments are based on empirical values and are carried out according to the principle of trial-and-error. Christian Witz from the Institute of Process and Particle Technology at Graz University of Technology explains this approach:
“At the moment, the biopharmaceutical industry still lacks an in-depth knowledge process. We know that the manufacturing process works, but we don’t know why and how it works.”
The solution to the dilemma is seen in simulation programs that allow for the systematic use of the knowledge process. Existing solutions require a mainframe computer, simulation expertise and months of computation time. They are therefore difficult to access, time-consuming and yet still do not make things much easier.
Systematization of processes
Issues that Witz wants to solve with his simulation software, which should:
- run on standard graphics processors;
- may be operated by persons without simulation training;
- have a simulation time frame of just a few hours;
The software shortens troubleshooting with this configuration and assures a better understanding of the process.
“Companies will need fewer trials to get from the lab to industrial production and will save between three hundred thousand and one million euros.” Christian Witz
The software is based on a simulation code for agitated and aerated bioreactors that Witz launched in 2017 and which is already being used in industrial research. The program simulates, for example, the motion of microorganisms in the reactor or the spread of oxygen released from air pockets.
Industrially applicable program
As part of the K-ComBioPro project – Computational BioProcess Design, he is now developing simulation technology into an industrially applicable program. Together with co-researcher Hans-Peter Schnölll, he plans to extend the functionality by a number of modules. The researchers also hope to partially automate the process of evaluating raw simulation data. The project will run until May 2021.
Through the implementation of additional algorithms, the physical and biochemical processes in the bioreactor will be mapped even more precisely and the system will become even more user-friendly. This should answer the essential questions that arise throughout the biopharmaceutical production process:
- Under which conditions is the productivity of microorganisms stimulated in the bioreactor ?
- What influence do the speed of the agitators or the aeration rate have on the process?
- Where do excessive mechanical shear forces affect the microorganisms in the reactor?
Answers to these questions will help companies to identify production losses that occur in the bioreactor within a considerably shorter simulation period.
Building block for Industry 4.0
Furthermore, an extended market and competition analysis will also support the preparation of business and financial plans.
The researchers see the technology as an important building block for the digitization of a more conventional industry and a building block for Industry 4.0.
With the help of a spin-off fellowship program from the Austrian Research Promotion Agency FFG, the two researchers are now able to set up their own company. The purpose of this company is divided into two sections:
- conducting simulations commissioned by biopharmaceutical companies and advising them;
- the marketing of software licenses to companies that do not share their data and who want to work with the program themselves;
The simulation algorithms are also compatible with other technologies and industries.
Also of interest:
Algae as a valuable renewable raw biomaterial
Yeast as an alternative protein source for animal feed