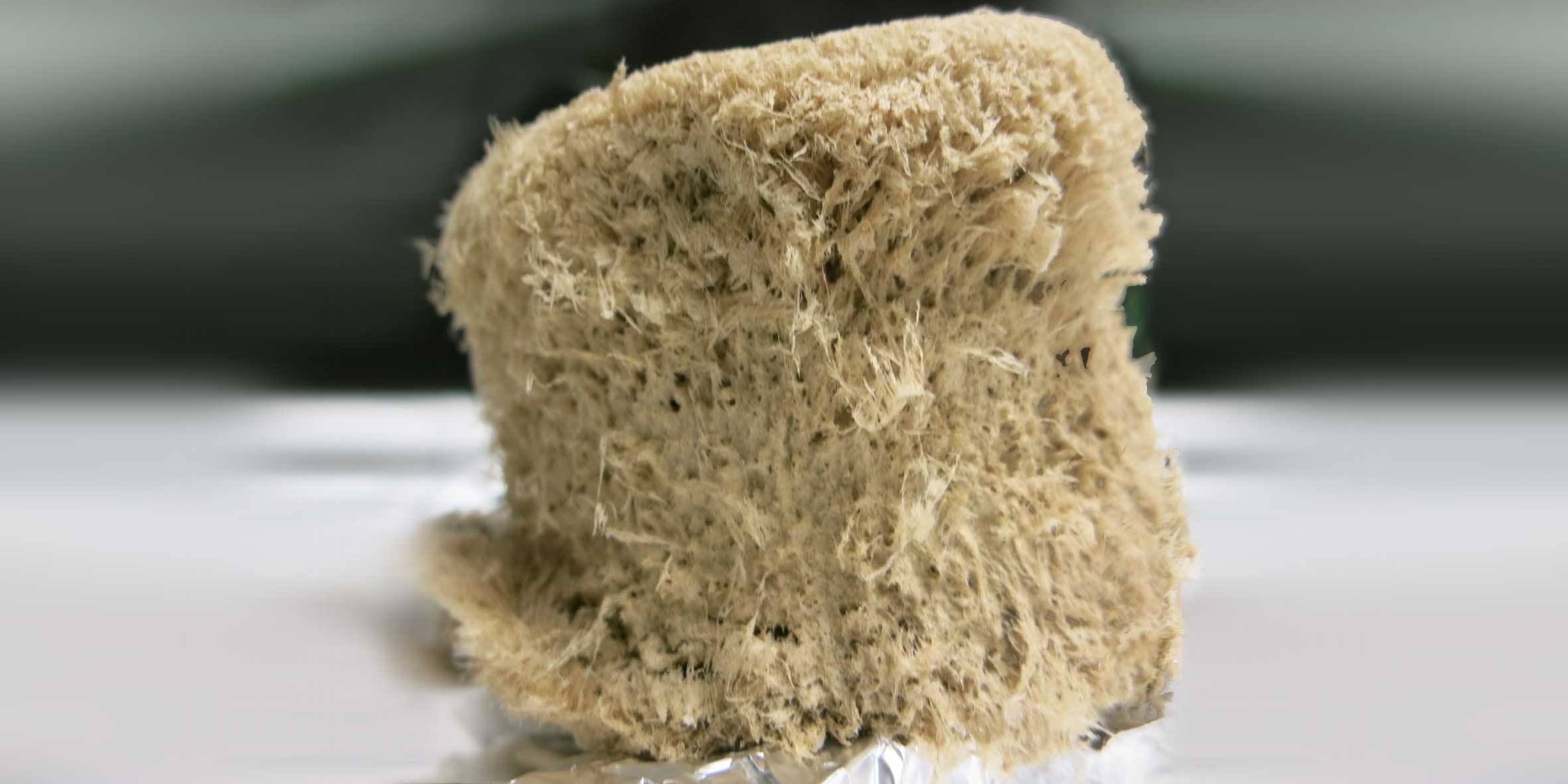
Fossil raw materials such as crude oil, natural gas and coal must be replaced in the long term by renewable materials if life on Earth as we know it is to continue to exist. Besides, these fossil raw materials will eventually run out. Wood, on the other hand, is a raw material that grows back again. As a renewable resource, it has great potential in the fight against climate change. On the one hand, it binds around one ton of carbon per cubic meter. On the other hand, it also represents an environmentally friendly alternative to fossil raw materials that are responsible for a large proportion of greenhouse gas emissions. That is why researchers at the Institute of Biobased Products and Paper Technology at Graz University of Technology, Austria, have started producing biodegradable materials from the wood components cellulose, hemicellulose and lignin.
To use less plastic and more biodegradable materials in the future, Samir Kopacic, who holds a doctorate in engineering, is researching novel packaging materials in the instituteโs so-called โBarrier Labโ together with academic and industrial partners. These bio-based materials should exhibit barrier properties that are just as good as synthetic plastics. In practice, this means that they must protect the packaging contents such as food, cosmetics, medicines, etc. just as reliably from oxygen, humidity and other external influences as conventional plastics do. In the case of foodstuffs, this is compounded by the fact that the flavor must be preserved in addition to the freshness of the products.
Prerequisites for a decisive breakthrough
Simply replacing plastic with paper or cardboard is not enough, however. โPaper and cardboard are porous and fibrous,โ says Kopacic. โTo achieve the necessary impermeability, they are often coated with synthetic polymers that are non-biodegradable and difficult to recycle or they are laminated with metal foils.โ He wants to change that in collaboration with Austropapier, the Association of the Austrian Paper Industry, and with the help of industrial partners.
Kopacic and his team are pursuing the goal of spraying paper or cardboard with biopolymers in the FFG research project โPapSpray.โ โWhen applying biobased barrier materials to paper, conventional coating processes have had limited success due to the complex flow behavior of these materials,โ explains project leader Kopacic. โWe are now testing the suitability of spray coating processes and investigating how biopolymers need to be sprayed onto paper to get the desired barrier properties.โ
The conditions for a decisive breakthrough are in place, he emphasizes: โFrom a technological point of view, the spray coating process is a flexible one that can be integrated into paper production and used in combination with or as a supplement to conventional coating technologies.โ According to Kopacic, the three-year research project, funded with โฌ810,000 as part of the EUโs โBreadCellโ project, aims to โdevelop a fundamental understanding of the interactions between paper, biopolymers and the spray process.โ This, he says, will create the foundation for producing and using plastic-free and recyclable paper packaging on an even broader basis in the future.
More than just packaging materials
In addition to innovative packaging materials, โBreadCellโ is focusing on various other projects such as the development of polymer foams made of cellulose manufactured without plastic for environmentally friendly lightweight materials based on wood or cellulose. Here, researchers from the Graz University of Technology, Austria; the University of Vienna, Austria; the Fundaciรณn Tecnalia Research & Innovation, Spain; and the Bionanonet Forschungsgesellschaft mbH, Austria; under the leadership of the Chalmers University of Technology, Sweden, want to develop a radically new technology for the production of environmentally friendly lightweight materials based on wood and cellulose.
At the moment, lightweight materials used, for example, for safety components in cars or for lightweight, robust and resistant sports equipment are made of synthetic polymers. โWe want to offer alternatives and are working on sustainable cellulose foams to replace existing composites,โ explains Associate Prof. Stefan Spirk. The project is supported by Hermann Steffan and Florian Feist from the Institute of Vehicle Safety, who are contributing their expertise in the field of crash-safe materials.
More articles on the topic can be found here.