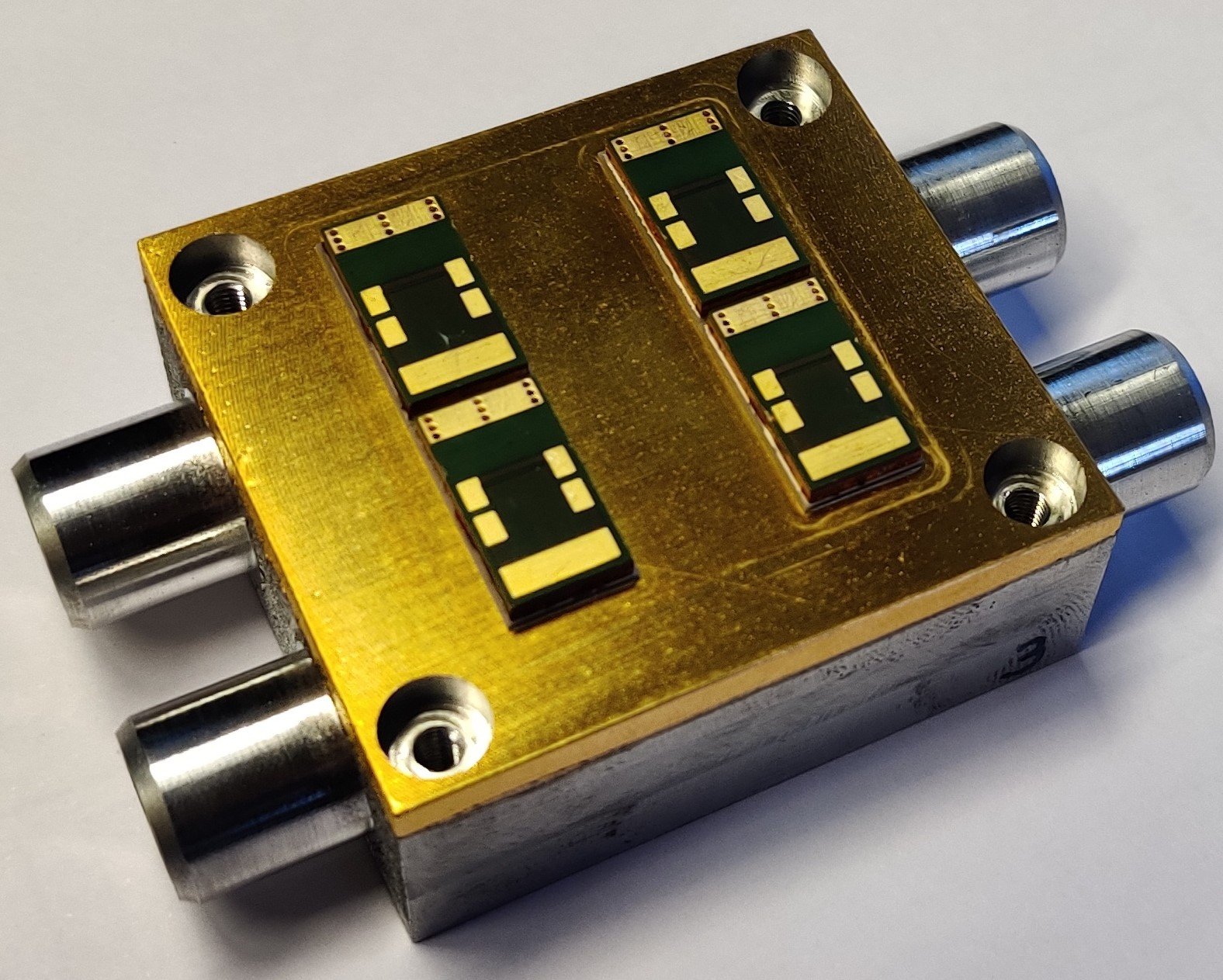
A major shortcoming of most electric vehicles is still their relatively limited range before the battery needs recharging. But the problem is not just insufficient storage capacity in the battery. The entire powertrain can also be improved, achieving a few additional kilometers. To this end, experts at the Fraunhofer Institute for Reliability and Microintegration IZM in Berlin are now developing a so-called inverter that converts the battery’s direct current into alternating current, which is used to drive the electric motor. Since this inverter is located between the battery and the motor, it easily becomes very hot, as do its transistors. To prevent this, it is necessary to dissipate the heat via heat sinks.
To do this, the scientists use especially efficient semiconductors made of silicon carbide (SiC) for the transistors. They experience much lower losses when heat flows through them. The disadvantage is that these semiconductors are very expensive, which is why as few transistors as possible should be used. But they would then heat up more because they would generate more power loss, so they have to be cooled particularly well. To better cool the semiconductor with the same power loss, experts have completely redesigned the cooling elements of the inverters.
Up to six percent greater range
During acceleration, braking and fast driving – when large amounts of current flow back and forth between the motor, the inverter and the battery – the greatest losses occur in the inverter. This is where SiC semiconductors come into play. They reduce these losses. “We expect that electric cars will ultimately have up to six percent more range thanks to this optimization of the powertrain,” says Eugen Erhardt, who is responsible for SiCeffizient at Fraunhofer IZM. Even if that doesn’t sound like much, six percent is considerable, because normally more batteries are needed for such a leap in performance in an electric car battery.
The inverters in electric cars are cooled using water, with the heat sink’s cooling rods, known as fins, protruding into the water and releasing the heat generated in the transistors. The heat sink for the SiC transistors was 3D printed and has relatively thin walls. Here, the transistors sit on a metal plate that is only a few millimeters thick, making them closer to the cooling water which in turn enhances the cooling effect. “To prevent the thin metal plate from bending under the load, the cooling fins are designed in 3D printing to support the metal plate like the columns in a dome,” the scientists explain. “This structure is so stable that the heat sink can withstand both the pressure of the cooling water and the forces that occur when the transistors sinter onto the heat sink.”
Not yet ready for series production
But another obstacle had to be overcome. The different materials that make up the power modules expand to different degrees when heated. The result is that stress occurs in the structure which can subsequently lead to material fatigue and the failure of the inverter. However, the thin metal plates of the new heat sink can compensate for this stress during heating or cooling by deforming slightly. This very flexible thermoelectric design protects the expensive SiC semiconductors and contributes to a longer service life.
Another advantage of the new inverter modules is that they are not connected to other electronic components via fixed copper traces, as is usually the case. “Instead, the assembly of the heat sink and SiC transistors is linked to the rest of the electronics with copper strands – flexible, fine copper wires”, the scientists point out. This, too, would reduce the voltage in the inverters.
The new inverter will be tested in the coming months by project partner Robert Bosch. Porsche will then install it in a newly designed powertrain that is fully adapted to the SiC structure. “It will still take some time before it is ready for series production,” says Eugen Erhardt. “First, we’re bringing everything together into a prototype. After that, the individual process steps will have to be optimized.”
Cover photo: Well-cooled and efficient – inverters for Porsche drives. © Fraunhofer IZM
More articles on the topic of batteries can be found here.