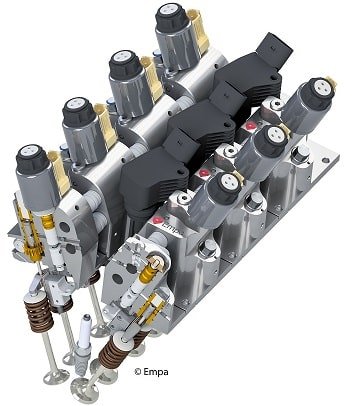
As long as combustion engines are available, it makes sense to optimize them as far as pollutant emissions and renewable fuels are concerned. One starting point involves using valves to supply and discharge these gases. Engine designers are specifically looking for a high degree of flexibility here in order to be able to improve efficiency, reduce pollutant emissions and make optimum use of renewable fuels. Up until now, the gas changeover valves of four-stroke engines have been controlled via camshaft drives. Despite sometimes complex additional mechanics, the versatility of such engines has remained limited. An electrohydraulically-operated valve train has now been developed at the Swiss Federal Laboratories for Materials Testing and Research (Empa). Its advantage: It enables full-on flexible adjustment of valve motion and timing. At the same time, it is robust and inexpensive to install. The Empa valve drive is based on a series engine. It has now been running successfully in an engine test stand for several months. So far results have shown that the new technology saves up to 20 percent more in fuel consumption in typical passenger car operating areas.
The valve train is the โrespiratory organโ of combustion engines: it controls the supply of new clean air and the release of exhaust gases, which is referred to as โgas exchangeโ. Today, only mechanically driven camshafts are used for this purpose in series production. These are often equipped with supplementary mechanics, some of which are quite complex. This in turn only permits the alteration of a valve motion pattern with increased friction determined by the camshaft. Flexibility is also not provided to the extent sought. What this means is that faster valve motion, stroke adjustments and cylinder selective variable valve timing are needed, among other things in order to adapt to alternating fuel properties even at low speeds.
Optimized gas exchange and reduced friction save fuel
Patrik Soltic, project manager at Empaโs Vehicle Drive Systems department, and his team have now invented just such an electrohydraulic valve train together with hydraulics specialist Wolfgang Schneider.

The system known as โFlexWorkโ developed by them is considerably more flexible than todayโs series technology. The valves are operated hydraulically and electrically controlled individually via a solenoid coil. As soon as a signal current flows, a specially designed hydraulic valve opens. This allows hydraulic fluid to open the gas exchange valve to the required stroke in milliseconds using a coil. If the current is switched off, the gas change valve closes again due to the force of the coil. It feeds most of the hydraulic energy that is required for this process back into the hydraulic system. The system uses significantly less energy than camshaft-driven systems over a wide operational range. Compared to conventional load controls using a throttle valve in combination with valve control via camshafts, fuel consumption of the test petrol engine is around 20 percent lower in the low load range that is typical for passenger cars. The researchers also paid attention to an optimized gas exchange.
Adaptable to renewable fuels
Opening- and closing time periods as well as the valve stroke for each cylinder can be independently set by selecting the relevant operational parameters. This allows any engine operating condition to be adjusted from operating cycle to operating cycle. This makes the engine highly adaptable to new renewable fuels: Oxygen-containing fuels such as methanol or ethanol allow more residual gas to be left in the cylinder. Natural gas, bio-gas and synthesis gas generated from wind and solar power have increased impact resistance. The valve train is also able to react flexibly to this phenomenon. In addition, alternative combustion concepts, such as (self-automated) homogeneous charge compression ignition, are able to be implemented relatively easily. A fuel-air mixture, for example, is ignited at the right moment without any sparks from the ignition itself by setting the correct conditions towards the end of compression and is thus burnt off virtually pollutant-free.
Cylinder head without oil
Another special feature of the system set up at Empa is the choice of hydraulic fluid: instead of using an oil as is customary, a water-glycol mixture, i.e. engine coolant, is used. Due to its physical properties, this mixture is very suitable for fast changing hydraulic systems, as it is quite solid and consequently results in less wastage. This makes the cylinder head completely oil-free, which can result in a simpler engine oil with longer change cycles occurring in the rest of the engine.
Several months of trial runs
This new valve train was put into operation in a natural gas-powered passenger car based on a VW 1.4l TSI engine as part of the FlexWork project backed by the SFOE. Requisite components were manufactured by Empaโs test workshop. The control system for the test engine was developed by Empa researchers themselves. The valve train has been running on an Empa engine test bench since October 2018 and has already withstood many millions of operations in heated engine conditions without any problems.
Another advantage is that the FlexWork valve control system only requires low-cost components. No expensive, fast-switching valves and no complex sensors are required. The valve train system was presented to experts at the Motor Technical Magazine (MTZ) on the 16th of August. Empa is currently in talks with engine manufacturers with a view to transferring this technology. Incidentally, this technology is not only suitable for combustion engines, but also for compressors.