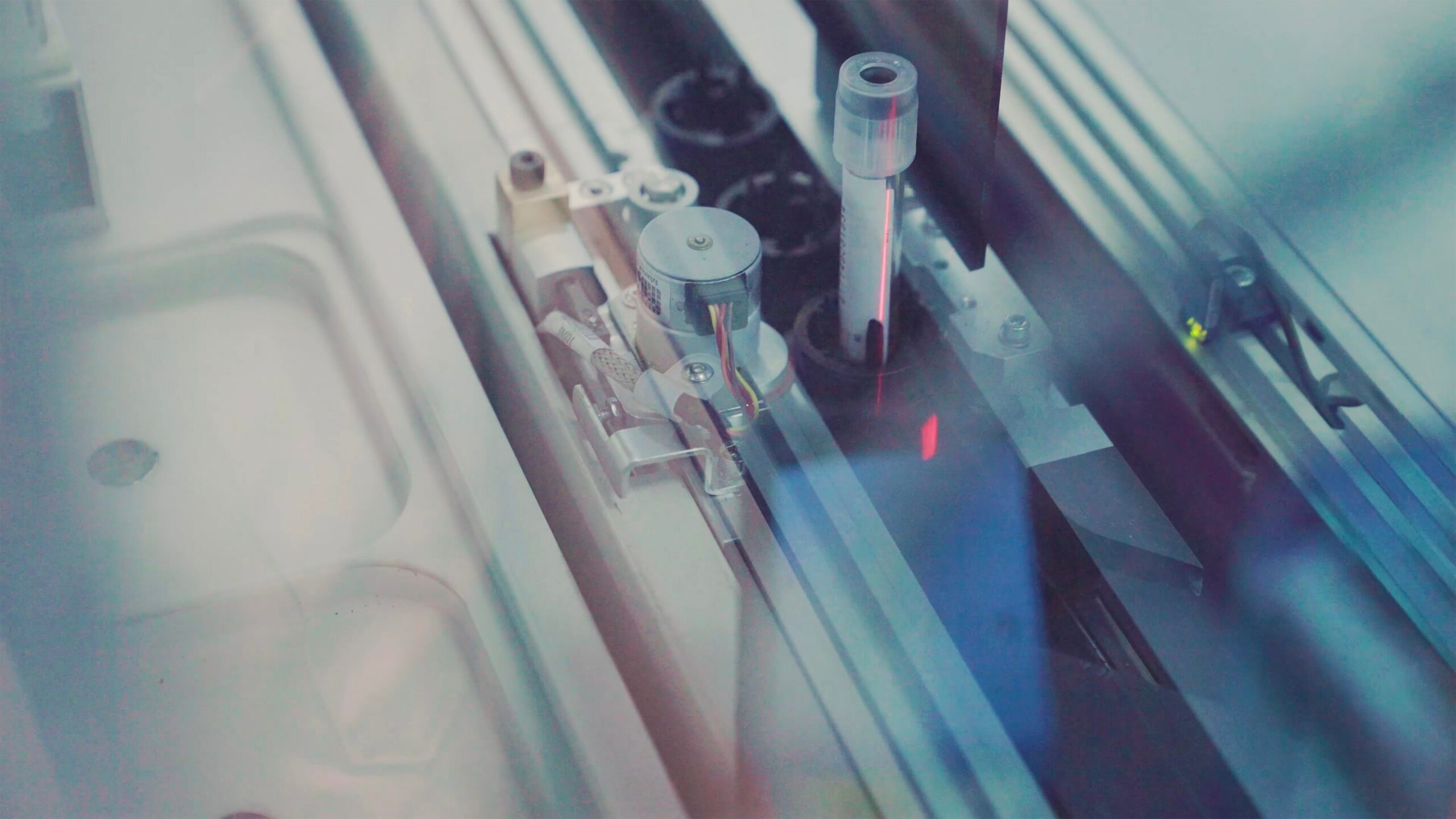
Medical analyses require state-of-the-art laboratories and the work of experts. Different substances have to be processed with complex equipment, cost-intensive chemicals and high personnel costs. At Johannes Kepler University (JKU) in Linz, Austria, they know how to do things differently. Several lab-on-a-chip platforms have already been developed there and are being used successfully. Examples include a pregnancy test and a rapid COVID-19 test. With the Lab on a Chip, analyses can be carried out directly at the point of care, meaning on the patient. The COVID-19 pandemic recently showed that this is an advantage.
Trial and Error
There is an urgent need for lab-on-a-chip solutions, especially in the field of cancer research and in the treatment of infectious diseases. These are especially needed in places with poor health care, such as developing countries. But chip lab development is delayed or prevented by costly and complex design and manufacturing processes. The process can drag on for months, requires micromanufacturing and, in some cases, manual labor. For example, channels must be dimensioned and connected. Also, the substances and chemicals used must be injected into the chip at the right pressure. Processes such as mixing, heating or incubation must be initiated at exactly the right time. Since the processes are carried out in the microliter range, even the smallest deviation can lead to a defective chip. Design and production therefore often succeed only through lengthy trial-and-error procedures.
Also interesting: โLab-on-a-Chipโ enables on-site analysis of lab results
A lab-on-a-chip must sometimes be completely redesigned even when just individual parts of tests are changed. โThis is because many medical tests differ in details, such as a slightly different incubation time,โ explains Professor Robert Wille, consortium leader and head of the Institute for Integrated Circuits at Johannes Kepler University in Linz and scientific director of the Software Competence Center Hagenberg.
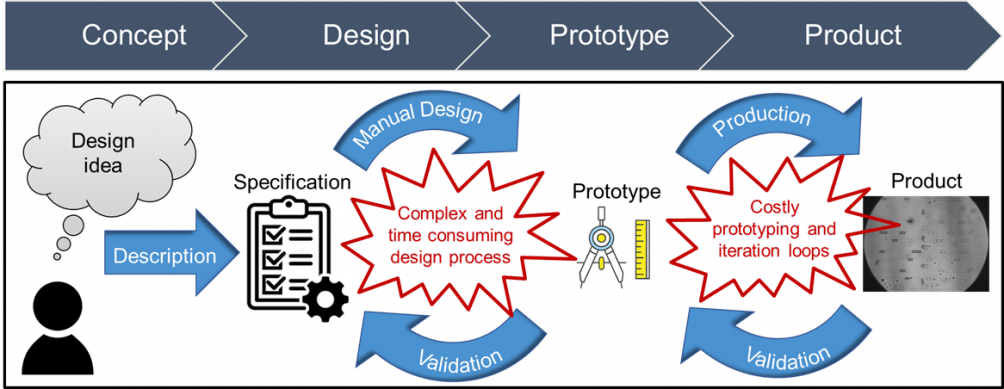
Microfluidic Systems
To simplify the design of the Lab on a Chip, a simpler design of these microfluidic systems is needed. Design automation using the laws of microfluidics can help. Here, liquids and gases are assumed to behave differently than macroscopic fluids in the smallest space. This is because effects that are often neglected in classic fluid mechanics can dominate at the smallest scales.
At Johannes Kepler University, research on microfluidics has been ongoing for many years. Several institutes are involved โ including mechatronics engineers, physicists and computer scientists. Research into the design and simulation of corresponding chips began about six years ago. The goal is to develop a process that can be used to convert laboratory procedures into corresponding lab-on-a-chip designs โ ideally at the push of a button. The aim is then to use this process as a basis for the large-scale fabrication of such systems.
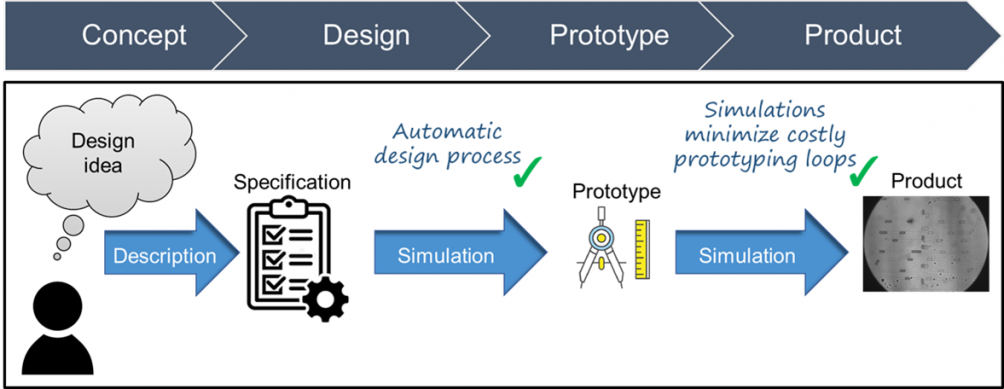
Calculations and simulations
Classic computer chips, which have highly complex units with sometimes millions or even trillions of components, are the role model. One example is transistors. These must be correctly placed and connected, among other things. Still, numerous automatic methods have already been established that make it possible to produce these chips at the push of a button. The consortium now wants to develop similar methods for chip labs.
โThe basics for this are known. We know from basic research how fluids behave in microfluidic systems. For example, how they are pumped through channels, how they mix when they branch, how long they flow through meanders, etc.โ Wille explains. But describing these processes requires complex mathematical principles and efficient computer programs that calculate and simulate the behavior. Simulation has the advantage of detecting possible errors beforehand on the screen. This means that the designs do not have to be produced before adjustments can be made. In a further step, methods and tools can also be developed on these bases that automatically generate at least parts of the design at the push of a button.
Construction of the tool
For the construction of the tool, different possibilities are being investigated. For simpler systems, it is sufficient to specify certain parameters such as the width and length of channels, the geometry of the system, the type of fluids used, etc. For more complicated systems, very detailed drawings of the system may have to be provided up front. โBut the advantage of a simulation is already clear here. You can quickly test whether the design works, quickly try out changes and correct errors,โ says Wille. This way design and production work can be reduced from several months to a few days.
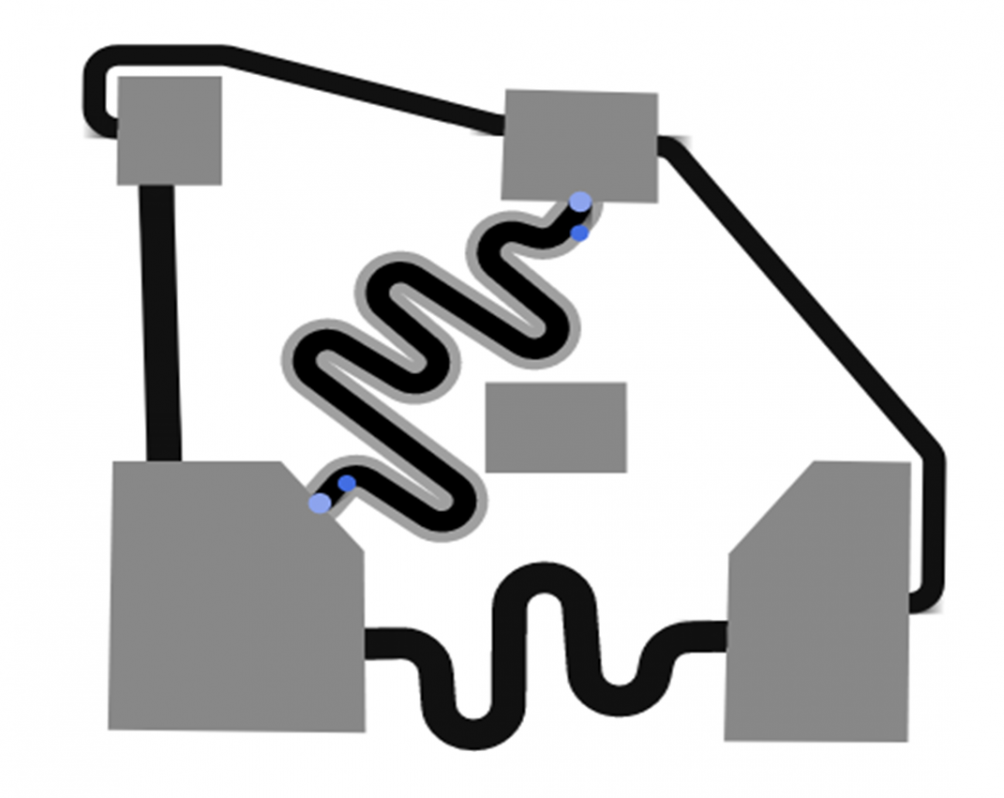
Automatic design
In the future, entire designs of microfluidic systems will be generated automatically simply by specifying the desired operations: liquids should be mixed, samples should incubate for a certain time, etc. An automatic tool sets up the corresponding system. Medical professionals are no longer necessary for the Lab on a Chip. Instead, engineers handle the individual steps on the chip.
This will make it easier to bring further medical analyses and examinations from the laboratory directly to the patient. Says Wille, โThis not only makes this technology cost-effective for many other applications but also allows us to respond quickly to new challenges, such as tests for new virus variants.โ
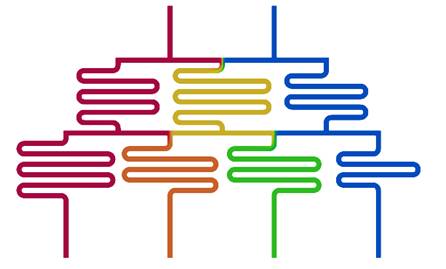
The consortium:
Several institutes at Johannes Kepler University Linz, Austria, are cooperating with ESS, Ernst Wittner Gesellschaft m.b.H. and the Software Competence Center Hagenberg. The Austrian Research Promotion Agency (FFG) is supporting the project with over โฌ1.4 million.