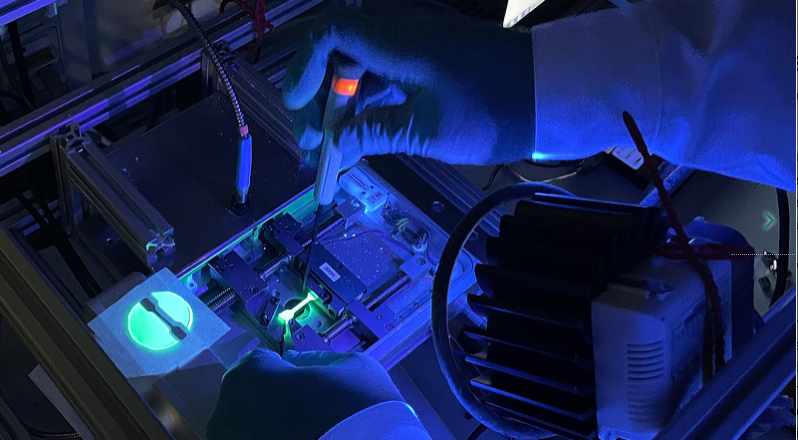
A research team led by Prof. Dr. Michael Sommer, who holds the Chair of Polymer Chemistry at Chemnitz University of Technology, and PD Dr. Michael Walter, project leader in the Living, Adaptive and Energy-autonomous Materials Systems (livMatS) excellence cluster at Albert Ludwigs University Freiburg, has succeeded in constructing a new dye molecule from the field of so-called mechanophores.
Thanks to this molecule, stresses on components can be displayed continuously by color changes depending on their intensity. The concept of such dyes is not new. However, previous mechanophores could usually only indicate the presence or absence of stresses in plastics. Current research now adds the additional dimension of the actual force of the stress. This offers major advantages wherever it is important to have an overview of stresses and thus also the integrity of the material at all times. The research team is now one step closer to developing this effective form of damage analysis and putting it to practical use.
The results of the study have been published in the scientific journal Nature Communications.
Molecular ‘spring’
As the researchers state in their publication, by combining a molecularly designed dye with a suitable and, above all, non-brittle plastic, macroscopic forces can now be applied on a molecular scale. These acting forces can be e.g. external pressure or tension.
The dye molecule thereby “feels” the force acting within the plastic. It then continues to indicate changes in force by changes in color. If the force on the plastic decreases, the dye molecule returns to its original state. Consequently, this dye is also called a molecular spring – it stretches and then “springs” back to its original state.
Compared to other existing molecular sensors, which can indicate forces in plastics by changing color, the advantages here clearly lie in the variable mapping of forces of different sizes and the spring-like behavior of the molecule. This means that it can be used over and over again.
A better understanding of damping
“This is a big step towards being able to directly visualize external stresses and residual stresses of plastics with simple analytics. This could really benefit the further development of materials with improved mechanical properties or in the field of 3D printing,” Prof. Dr. Michael Sommer summarizes.
But it could also make it easier to understand the damping properties of special materials and as well as natural systems. For example, some large and heavy fruits fall from trees from great heights, but survive the fall undamaged. Nature serves as a model here, and molecular springs could help to better understand and imitate such systems.
Future efforts will consequently focus on adapting molecular force springs for use in various polymers. This will involve cooperation with other research groups along with the use of computer-aided methods.
Photo: The developed dye indicates stresses and their strength in plastics and components. Whether this works in practice was studied in mechanical experiments using a test body with a force spring.
Also interesting: Detecting environmental damage in forests with drones and sensors