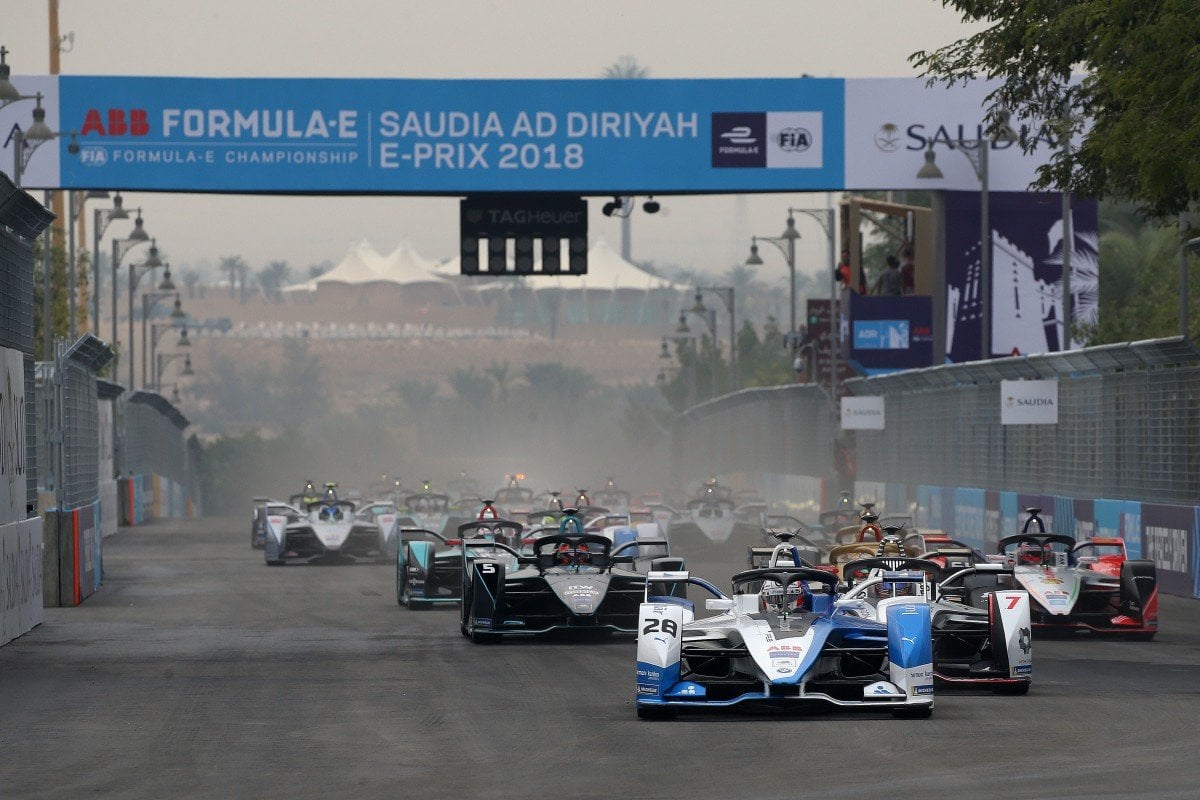
In its first season (2014/15), Formula E had quite a modest start. All ten teams had identical cars, the Spark-Renault SRT_01 E from Spark Racing Technology, a company set up by Renault specifically for this purpose. Italian carmaker Dallara supplied the chassis, McLaren Electronic Systems supplied powertrain and electronics. The Williams Advanced Engineering battery weighed 200 kilograms and delivered a maximum of 28 kilowatt hours at up to 1000 volts; the season 1 engine produced 200 kW (272 hp) and the cars had a maximum speed of 225 km/h. The teams were not allowed to develop their cars, that was only possible from season 2 – and a lot has happened since then.
Over the years, the battery performance has been continuously increased, but the car change in the middle of the race has still highlighted the shortcomings of the new technology: the fact that electric vehicles simply lack range, whether on the race track or on the road. However, since the first race of the fifth season in the streets of Riyadh on December 15, 2018, this has finally changed – at least on the racetrack.
The eleven teams that make up the grid in the 2018/19 season, start with the new SRT 05e standard chassis from Spark Racing Technology. The standard Williams battery that was used in the first four seasons has been replaced by a 348-kilo battery pack from McLaren Applied Technologies. Michelin still supplies the standard tires. All other components such as the engine, transmission, suspension, springs, shock absorbers, stabilizer, brake-by-wire system, and cooling system can be developed by the manufacturers themselves. In addition, the maximum output of the vehicles has been increased from 200 kW/272 hp to 250 kW/340 hp, which means that the acceleration from 0-100 km/h only takes 2.8 seconds. The cars’ maximum speed is now 280 km/h. The battery capacity is now at 54 kWh.

These new possibilities for self-development and above all the omission of the car change in the middle of the race are attracting new manufacturers into Formula E. Besides Renault, Audi, Venturi, Jaguar or Mahindra, Mercedes is now doing a test year under the HWA flag. Nissan has taken over DAMS and renamed it Nismo-Team, and BMW has taken over Andretti. “Formula E is not only an innovative and spectacular race series that has established itself as one of the top race series in the world with a totally new approach to sustainability and events within just a few years,” said Klaus Fröhlich, Member of the Board of Management of BMW AG, Development and Motorsport, at the presentation of the BMW iFE.18 on 14 September 2018 in Munich. “For BMW, it is also the perfect test lab for production development. The technology transfer between motorsport and series production is intense. Our experience from series production benefits the drivetrain of the race car. At the same time, insights from Formula E flow directly into the development of future series production drivetrains. So, I am looking forward to a great racing season.”
In part, the BMW iFE.18 was built at the same production plants as the BMW i3 and the findings from Formula E flow directly back into the development of future series production drivetrains of forthcoming BMW i models. “BMW’s expertise in the BMW iFE.18 is primarily in the heart of the vehicle, the drivetrain,” said BMW Motorsport Director Jens Marquardt. “We told the production engineers designing the electric motor and inverter: ‘Forget about all the considerations you would usually have in development, and just think about performance, the greatest efficiency, the lowest weight. When we’ve reached that point, you can think about how to integrate that into series production later on.’”
The engineers then designed the rear-axle including suspension and had to integrate the drivetrain in the rear end of the race car. “The knowledge we gain in this highly competitive environment then flows straight back into production development. This is the perfect implementation of our motto: from the racetrack to the road,” emphasized Marquardt.
The drive train
The “heart” of the new BMW i Andretti Motorsport racer is the drive train, the Racing eDrive01, which consists of the electric motor, cooling system, and inverter.
The electric motor is essentially made up of three parts: The rotor, the stator, and the casing. The rotor has supports made of fiber composites, which contribute to reduced weight and strengthening. In addition, there are innovative materials such as highly thermally-conductive resins, titanium, and ceramic.

The cooling of the electric machine is achieved by a virtually 360° cooling geometry in aluminum casing manufactured via the additive manufacturing procedure. In addition, highly thermally conductive materials such as ceramics and casting resins contribute to the cooling.
The inverter converts the direct current from the standard battery into the alternating current that powers the electric motor. The casing is partly made of fiber composites; inside the semiconductors are multiple MOSFETS (metal-oxide-semiconductor field-effect transistors) with state-of-the-art silicon carbide technology. Thanks to this technology, the inverter achieves a very high dielectric strength with minimal energy loss and is thus also smaller and lighter. An effective cooling system and a loss-optimized circuit layout also contribute to the inverter’s maximum efficiency.
Rear structure and rear suspension
In addition to the drive train, the rear-end of the car and the rear suspension are the areas where manufacturers have the greatest leeway for their own developments, which is why the rear axle – including suspension and shock absorbers – is also a complete BMW in-house design on the BMW iFE.18. This means that the team can individually adjust the suspension, depending on the track characteristics, i.e. the setup parameters such as spring rates, anti-roll bars, ride height, toe, and camber.
Other than the mostly smooth surfaces of permanent race tracks, city circuits are usually much more uneven, which means that the setup plays an important role in achieving maximum mechanical grip. On road circuits, it is also, especially that both the chassis and the rear structure are robust enough to cope with driving over aggressive curbs and light contact with the track’s barriers. By the way, various components were produced using the 3D printing procedure – as is now quite common in racing.

Brake-by-wire system
Another in-house development of the Munich carmaker is the electronic, brake-by-wire braking system, which represents a major technological step for Formula E and, in this regard, takes it to the same level as Formula 1 and the LMP1 category in the FIA World Endurance Championship (WEC). Brake-by-wire controls the relationship between mechanical braking force when the driver pushes the brake pedal, and the braking effect generated by energy harvested during deceleration and braking. When the motor recovers energy from the braking process during the race, it basically functions as an additional brake on the rear axle of the car.
Thanks to the brake-by-wire system, drivers no longer have to adjust the brake balance manually to balance the additional braking effect. The electronics now perform this balance and automatically feed the maximum amount of energy back into the battery when braking. This additional energy also helps to ensure that the cars can complete an entire race distance with the limited amount of energy from the batteries at maximum power and not retire prematurely due to empty batteries.
Will Porsche be followed by Ford and Ferrari?
In season 5, Formula E has already raced in Riyadh, Marrakech, and Santiago de Chile. The first winner of this season’s “new Formula E” was Portuguese driver António Félix da Costa, who drove his BMW to victory in Saudi Arabia – and motorsport boss Jens Marquardt sang praises to his team. “On the track, we have also shown that BMW is one of the world’s leading manufacturers in terms of electromobility. This success gives a great boost to our series and motor racing developers,” he said.
However, in the following two races, Da Costa and his British team-mate Alexander Sims had to set their sights lower – and in the 2019/20 season, it will get more difficult for everyone. As of season six, Mercedes and Porsche will enter their own factory teams. In addition, Ford is obviously thinking more and more seriously about entering Formula E and maybe even Fiat/Ferrari will come. The late Ferrari President Sergio Marchionne declared already in 2017 that Ferrari “needs Formula E”.
“We need to be involved in Formula E because electrification via hybridization is going to be part of our future,” Marchionne told Auto, the FIA’s official magazine. “Hybridization is crucial to Ferrari. There is no denying that regulations put us under pressure, but we could reach those targets in other ways,” he explained. “The challenge is to benefit from hybridization not just in terms of emissions reduction, but also performance. We have already developed a hybrid supercar, La Ferrari, and on future Ferrari models we will leverage new technologies as well as electrification.”
However, both Ford and Ferrari would have to team up with one of the existing teams, as the number of teams is limited to twelve and Porsche will complete the grid in season six.
On February 16, the Mexico City ePrix will be the fourth race of the season, and, alongside Monaco, will be the only race to be held on the same circuit as Formula 1. On May 25, Formula E will race in Berlin for the fifth time in its history, this year again on the grounds of the former Tempelhof Airport. The final race weekend of the season with races number 13 and 14, will take place in New York on July 13-14.
Part one of our two-part series about Formula E can be found here:
Formula E: From “Nonstarter” to Crowd-Puller
Cover picture: © BMW