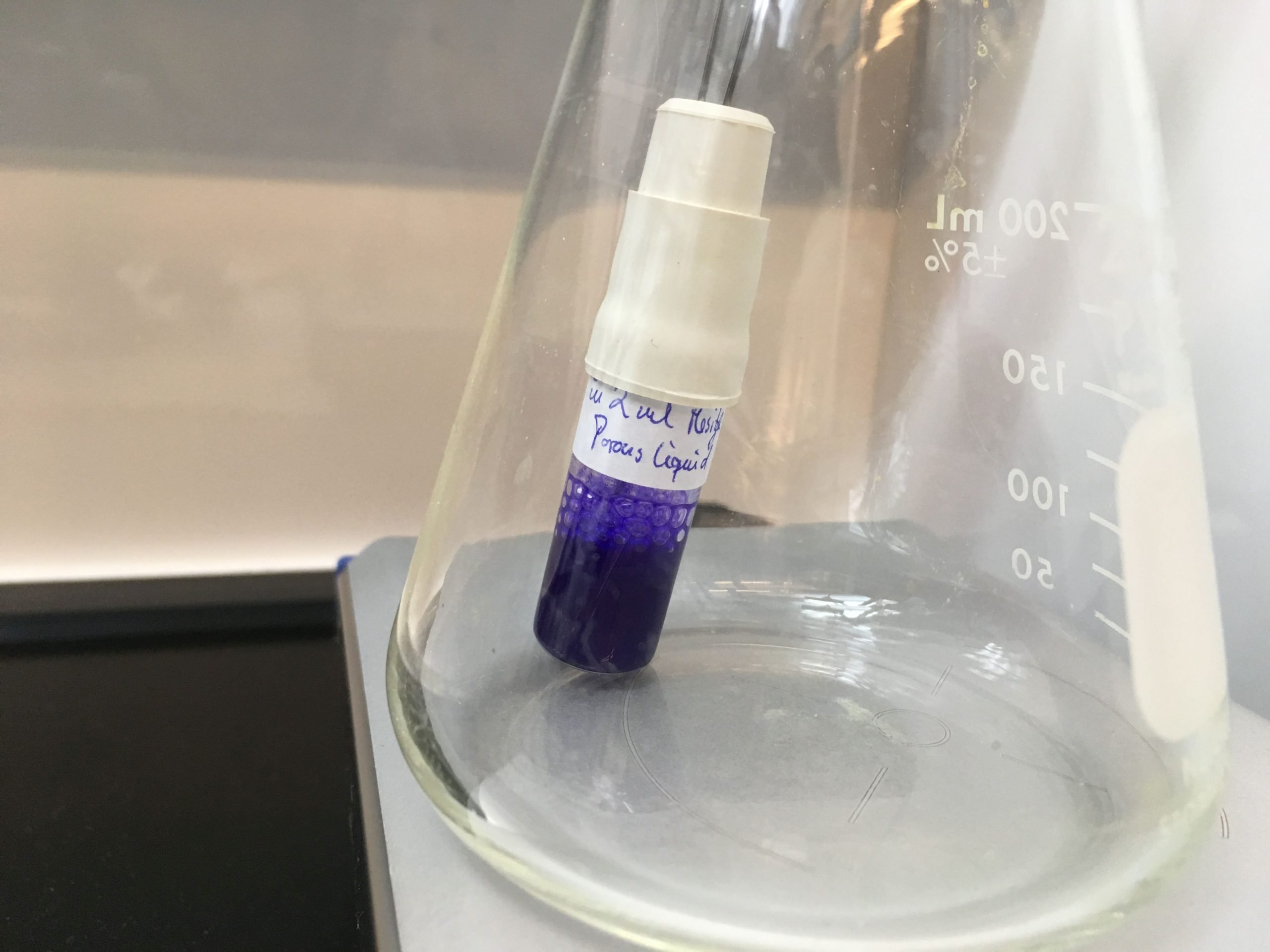
In simple terms, distillation is the process of separating liquids from each other using a thermal process. This enables the recovery of evaporated liquids for one thing. In addition, solvents can be separated from substances that are difficult to evaporate and which are then recaptured via condensation. Although this traditional process is very effective, it is nevertheless energy-intensive.
Scientists at the German Karlsruhe Institute of Technology (KIT) have now developed a process that might make distillation obsolete. All thanks to new ‘porous liquids.’ This process entails letting nanoparticles float in a solvent which separates gas molecules of varying sizes from one another. This is accomplished when empty pores in the particles have apertures that only molecules of a certain size can pass through. Larger molecules remain on the outside and are separated from the smaller ones this way. The researchers explain that these porous liquids could be used directly, but they could also be turned into membranes, “which are able to efficiently separate propene from gas compounds as the raw material for the widely used plastic polypropylene.”
Propene is for the most part extracted during the refining of crude oil or natural gas in a distillation process that separates it from other gases and purifies it. Propene is one of the most important raw materials for the production of polypropylene in the chemical industry. This plastic is mainly used for packaging materials and in the construction and automotive industries.
Greenhouse gases reduced by a factor of five
“In the technical literature, it is assumed that gas separation in petrochemistry using membranes would only cost one-fifth of the energy required for distillation,” says Dr. Alexander Knebel, head of the junior research group at the Institute of Functional Interfaces (Institut für Funktionelle Grenzflächendes, KIT), who was conducting research at Leibniz Universität Hannover in Germany and in Saudi Arabia until 2019. “In view of the required high quantities of propene, this means that the release of huge amounts of the greenhouse gas CO2 can be avoided.” Therefore, the petrochemical industry in particular could benefit from using membranes instead of distillation for the separation of propene. In trials carried out by Knebel and his colleagues, the flow rate of the new membranes was at least three times higher than that of existing materials.
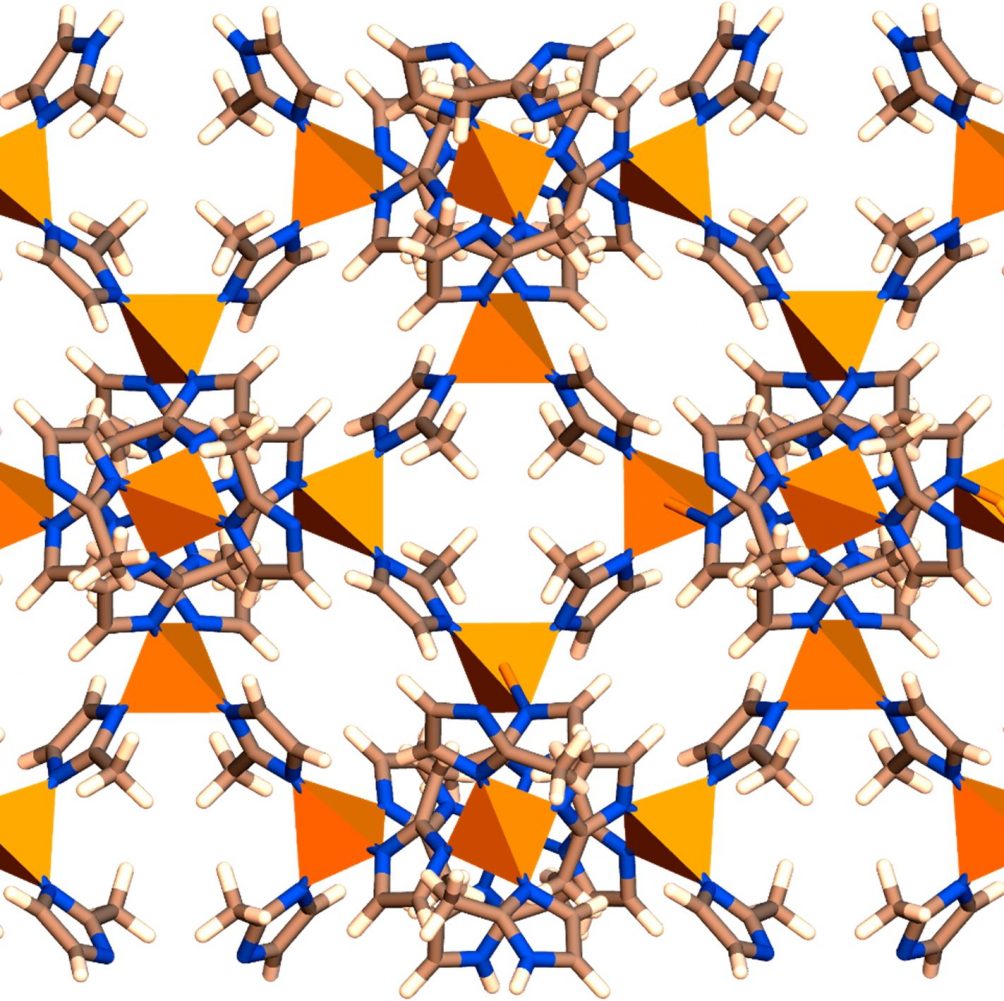
The starting point for the research focused on the solid material ZIF-67 (Zeolitic Imidazole Framework). Its atoms form a metal-organic network with 0.34 nanometer-wide aperture pores. The researchers succeeded for the first time in “finely dispersing a metal-organic framework in liquids such as cyclohexane, cyclooctane or mesitylene” by specifically modifying nanoparticles of ZIF-67 on the surface. The scientists have dubbed the resulting dispersion: ‘porous liquid‘.
Gaseous propene takes considerably longer to pass through a column filled with the porous liquid than methane, does Knebel goes on to explain. This is because propene is effectively captured in the nanoparticles’ pores, whereas the smaller methane molecules are not. “We want to exploit this property of the dispersion in the future to produce liquid separation membranes.”
Degree of purity at least 99.9 %
According to the researchers, the porous liquids can also be used to produce solid separation membranes which have exceptionally advantageous properties. For example, in membranes made from a plastic substance and the chemically modified ZIF-67 whereby the team succeeded in increasing the proportion of modified ZIF-67 in the membrane to 47.5 %. They achieved this without making it physically unstable. In a gas compound comprising equal parts of propene and propane, which was then passed over two membranes connected in series, the result was propene with a degree of purity of at least 99.9 %. “Even though the two gas molecules only differ by 0.2 nanometres in size,” according to the scientists.
The decisive factor that determines the effectiveness of these membranes entails as many metal-organic particles as possible to be uniformly distributed throughout the plastic. And that the pores in the nanoparticles are not blocked by solvents during membrane production. In other words, that they remain empty. “We were able to achieve both goals because we did not directly incorporate solid particles into the membrane, but instead proceeded via the porous liquids even though this looks like a detour,” Knebel elaborates.
Schnapps or disinfectant?
However, the new process is not only interesting for the petrochemical industry. It can also be used in the production of alcohol. Basically, distillation could also be replaced in this area, Knebel claims. “In principle, that would be possible. Presumably, it could be done with a polymer membrane, and not by using a porous liquid directly. Then the process would be called pervaporation rather than permeation.”
However, the researcher foresees difficulties with alcoholic beverages such as gin, rum, or suchlike. “What I find problematic here is that you would want fusel alcohols and highly volatile substances to have some influence on the taste/odor, which only happens during distillation,” he points out. “With membrane distillation, they would be totally eliminated and the product would end up as very pure alcohol.” But that’s also fine if you wanted to manufacture disinfectants, for instance. “Energy savings would be similar to what you can achieve with gas separation.”
Knebel and his colleagues from Leibniz University of Hanover, King Abdullah University of Science and Technology (Saudi Arabia), and the Deutsches Institut für Kautschuktechnologie (German Institute for Rubber Technology) reported on the results of their research in the academic journal Nature Materials.
Title image: Porous liquids acting as membranes: This process could save enormous amounts of energy and consequently cut down on CO2 in the plastics industry. (Photo: Alexander Knebel, KIT)