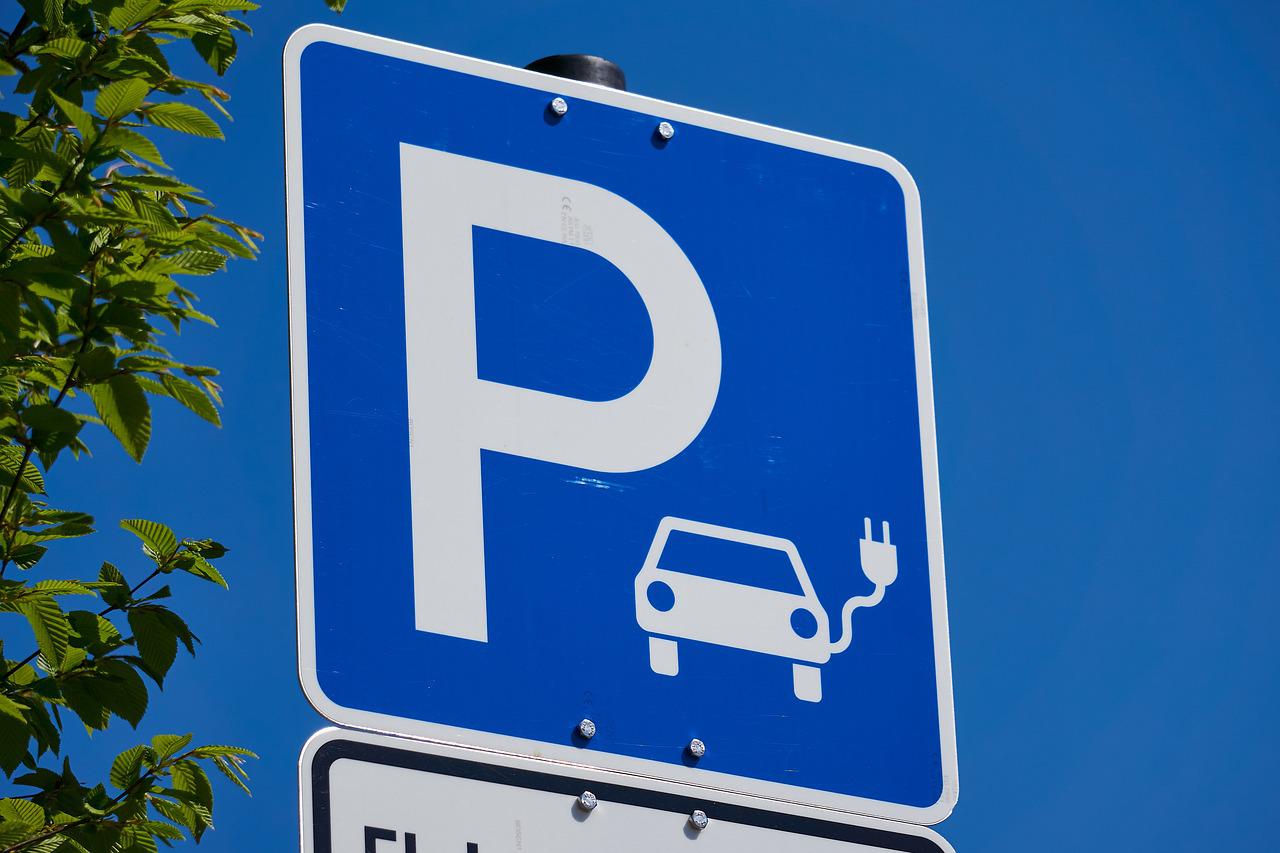
With a share of 30 percent, the transport sector is one of the largest CO2 emitters. Conventional vehicles with combustion engines are to blame. Battery-powered electric vehicles, on the other hand, cause hardly any local emissions. They could make a significant contribution to achieving climate targets if it weren’t for the production of the batteries, which, according to a Swedish study, generates 61 to 106 kilograms of CO2 per kilowatt-hour.
State-of-the-art are lithium-ion batteries, which combine both lightness and high density. As a result, the metal can store a lot of energy per kilogram of battery weight – more than other battery materials. Since energy density is synonymous with range, lithium-ion batteries achieve greater ranges compared to other batteries at an acceptable resource cost.
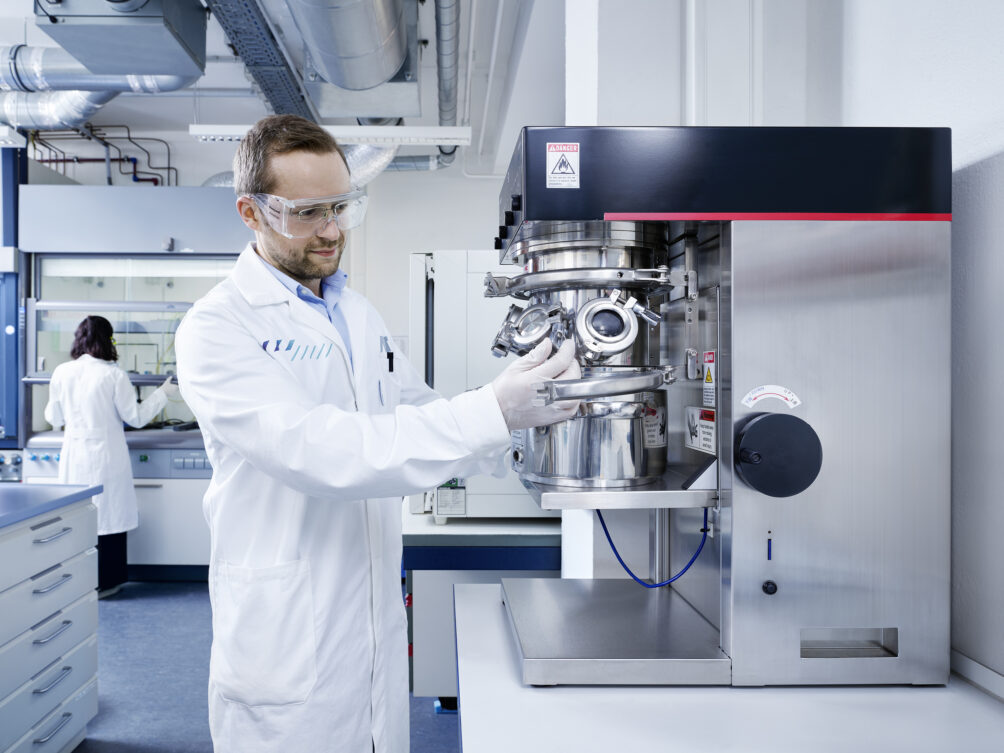
The problem with lithium-ion batteries is the liquid electrolytes that act as a conductive medium between the positive and negative poles, or anode and cathode. In the event of mechanical impact, such as in the event of an accident, this electrolyte fluid can escape and evaporate to form highly flammable gases.
The solid-state battery, on the other hand, doesn’t need any liquid electrolytes at all. It is therefore safer, explains Dr. Marcus Jahn, who heads the newly established Competence Center for Battery Technologies at the AIT Austrian Institute of Technology in Vienna, Austria.
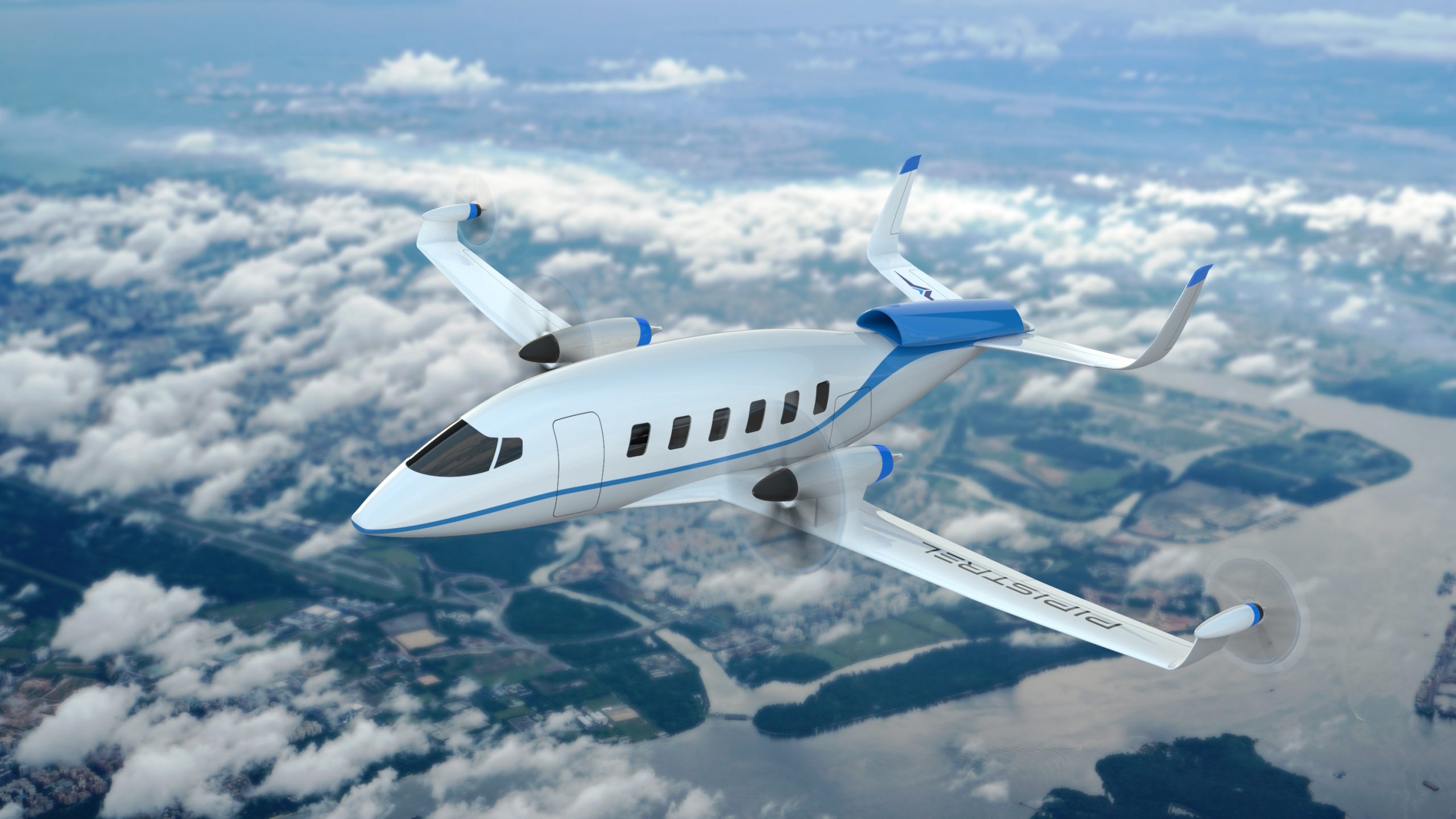
Solid-state batteries
But the manufacturing processes of solid-state batteries are currently still in the development stage. Only a few research groups in Europe are working on them. With the newly-founded Competence Center for Battery Technologies, the AIT is contributing to this still-emerging research. Existing research activities are being bundled and combined with new strategic topics. The aim is to create a kind of future laboratory that will advance battery technologies in Austria and Europe.
However, the solid-state battery is only one focus area of Jahn’s 30-member research team. It is still unclear which battery types for electric vehicles will prevail in the future, which is why the boundaries of the research field are relatively broad and include the search for new materials and manufacturing processes.
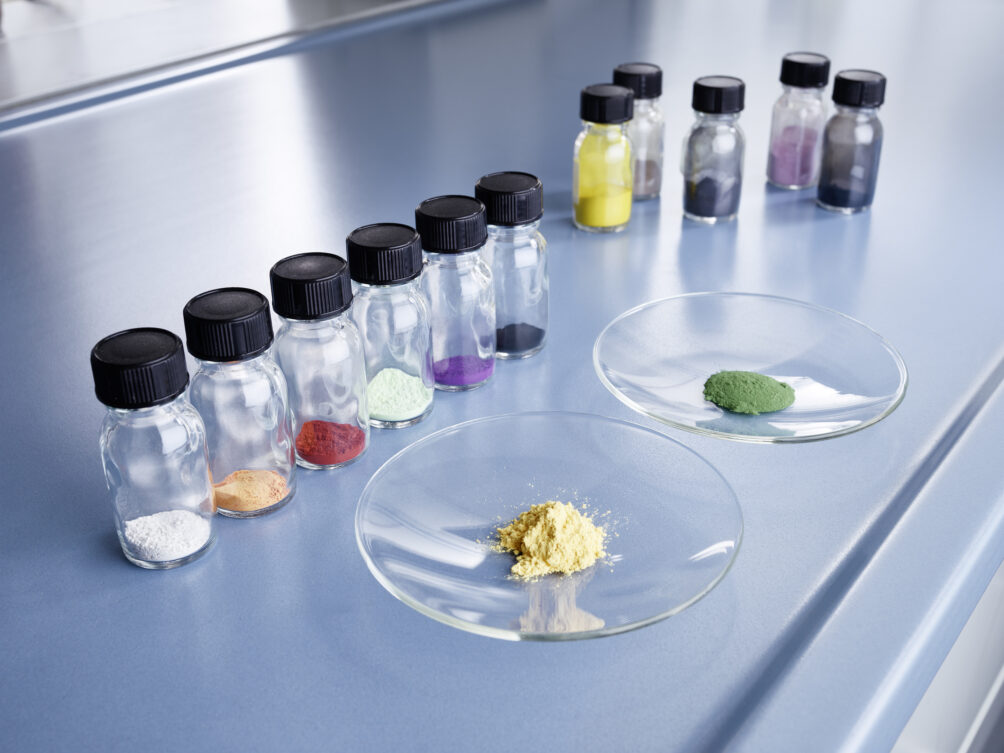
Cost, energy density, safety and sustainability are parameters that are important for all battery types and applications, Jahn explains. In the case of energy density, a distinction must be made between weight and volume, but in principle, different areas of application have different requirements. For example, weight and safety are crucial for airplanes, whereas costs are crucial for passenger cars.
What comes after lithium?
In the development and characterization of materials for batteries, the AIT researchers are looking for alternatives to critical raw materials. First and foremost on this list is lithium, which is highly reactive and easily combustible. Lithium-ion batteries are also associated with a rapid aging process. Current technology only guarantees seven to eight years for a battery pack. But annual figures are essentially obsolete because it is known that the speed of aging processes depends on the type of use and particularly the type and quantity of charging and discharging processes. This is because the latter cause gas formation and chemical reactions are never loss-free and cause aging, Jahn explains.
Possible alternatives for the future include magnesium-ion batteries or sodium-ion batteries. It is already known that these principles work and can be attractively priced, but there is still a lot of development needed. The same applies to cobalt, the main component of the electrodes, which should be replaced by alternative materials.
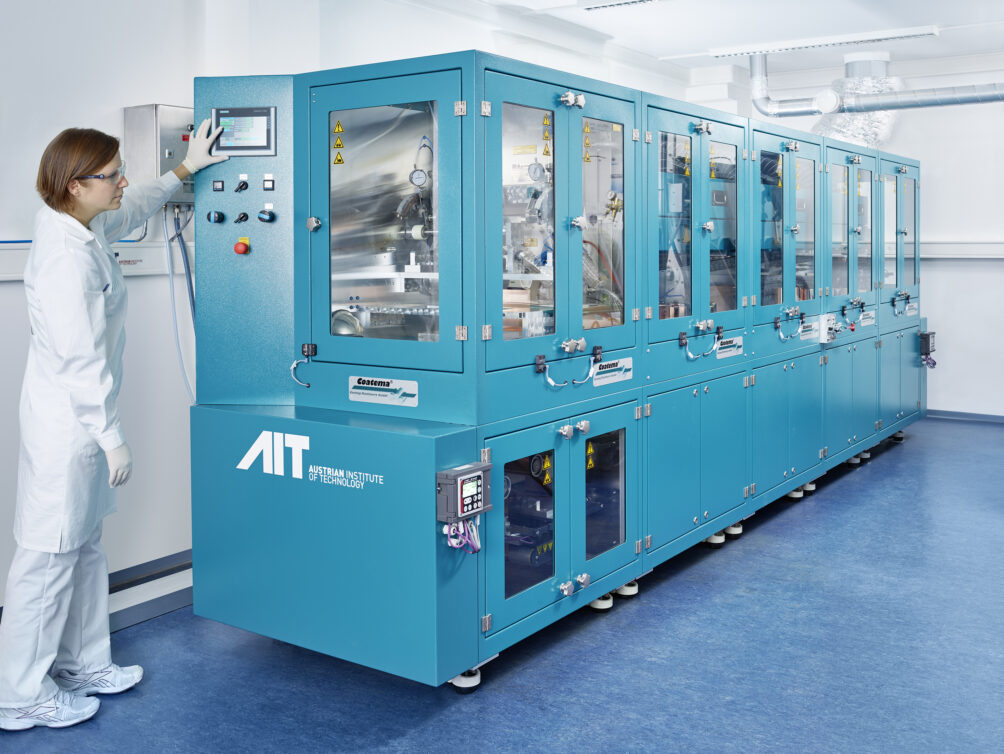
Sustainable manufacturing
In the research field of sustainable and intelligent battery manufacturing, AIT researchers are primarily concerned with methods for the industrial production of batteries for electric vehicles. In recent years, high-quality research infrastructure has been built for this purpose, including prototype production close to industry in which all processes are intensively investigated and can be further developed. A central focus is sustainable production which aims to replace environmentally harmful solvents with harmless substances, for example.
A battery essentially consists of electrodes, cathodes and anodes. Currently, electrodes are applied to cathodes and anodes as pastes, which traditionally contain toxic solvents, even if vapors have been eliminated. The ideal battery of the future, however, should consist of dry electrodes and thus be solvent-free. This has already been achieved with anodes, but there is still room for improvement with cathodes, Jahn said, adding, “It won’t be a green battery until it’s produced solvent-free, with low energy consumption and with sustainable materials.”
Pastes
The reason the solid-state battery is incomparably safer than the conventional lithium-ion battery is that it does not require any liquid electrolytes at all. It is also expected to have a greater range because solid electrolytes potentially have a higher energy density.
Suitable materials for solid electrolytes are already known; each has advantages and disadvantages. At AIT, the focus will be on polymers, ceramics and glasses or sulfide-based substances, among others. Based on this knowledge of materials, completely new manufacturing processes must be developed. This is because, unlike lithium-ion batteries, the production processes for solid-state batteries are not yet standardized and reproducibility is not yet a given. “To better understand these systems, fundamental questions still need to be answered,” Jahn explains.
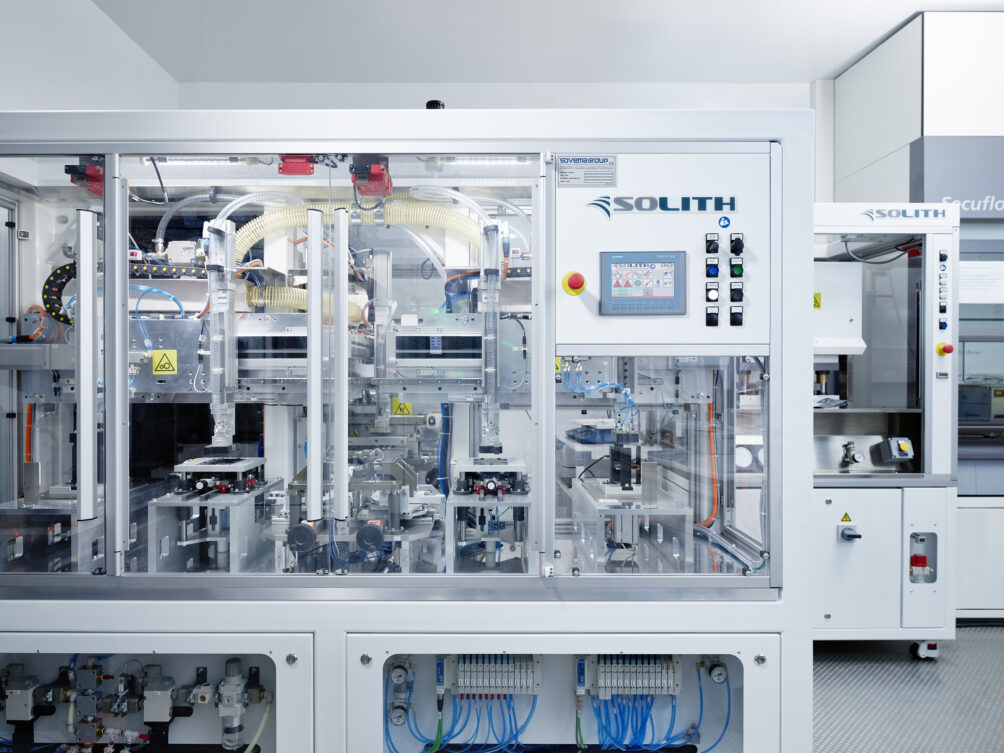
Transitional technology
Semi-solid batteries, which use a hybrid approach, are considered a transitional technology and use a gel-like substance. Liquids are added to this, which are then absorbed. Since the electrolyte is not liquid, it cannot leak, guaranteeing safety. But the ideal battery of the future should be solid. Only then is the high energy density possible, explains Jahn.

Life cycle analyses are carried out for all research areas in AIT’s new Battery Technology Competence Center. These cover the entire process chain from raw materials to production and use to the end of use and the use of recycled materials.